Dry Construction Market Size, Share, Industry Trends and Forecast to 2033
This report provides a comprehensive analysis of the Dry Construction market, including insights on market size, growth rates, segmentation, and key players. It covers data forecasts from 2023 to 2033, highlighting technological trends and regional dynamics.
Metric | Value |
---|---|
Study Period | 2023 - 2033 |
2023 Market Size | $1.80 Billion |
CAGR (2023-2033) | 6.2% |
2033 Market Size | $3.34 Billion |
Top Companies | Saint-Gobain, Knauf, USG Corporation |
Last Modified Date | Invalid Date |
Dry Construction Market Report (2023 - 2033)
Dry Construction Market Overview
What is the Market Size & CAGR of Dry Construction market in 2023?
Dry Construction Industry Analysis
Dry Construction Market Segmentation and Scope
Request a custom research report for industry.
Dry Construction Market Analysis Report by Region
Europe Dry Construction Market Report:
Europe currently represents a substantial share of the market, projected to grow from USD 0.52 billion in 2023 to USD 0.95 billion by 2033. The European Union's focus on sustainability and energy conservation fosters a favorable environment for dry construction techniques. Emerging legislation targeting reduced carbon footprints is propelling the market as construction companies seek compliance while maintaining efficiency.Asia Pacific Dry Construction Market Report:
The Asia-Pacific region is experiencing rapid urbanization, with the dry construction market projected to grow from USD 0.33 billion in 2023 to USD 0.62 billion by 2033. Major economies, such as China and India, are investing heavily in infrastructure, bolstering demand for efficient building techniques. Adoption of sustainable construction practices further drives the market as governments push for environmentally-friendly solutions.North America Dry Construction Market Report:
North America showcases a strong demand for dry construction, with market size anticipated to rise from USD 0.69 billion in 2023 to USD 1.29 billion by 2033. The region emphasizes smart building trends and innovative construction methodologies, with significant investments flowing towards residential projects. The push for energy-efficient homes and buildings enhances the appeal of dry construction technologies.South America Dry Construction Market Report:
In South America, the market is expected to escalate from USD 0.12 billion in 2023 to USD 0.23 billion by 2033. Regional economic developments, particularly in Brazil and Argentina, are fostering growth in the construction sector, supported by conscious efforts to improve building quality and efficiency. Dry construction methods are becoming increasingly relevant as they align with local sustainability objectives.Middle East & Africa Dry Construction Market Report:
In the Middle East and Africa, the dry construction market is expected to progress from USD 0.13 billion in 2023 to USD 0.25 billion by 2033. The region's booming real estate sector, propelled by both commercial and residential projects, offers extensive opportunities. Innovations in modular construction and efficient materials are recognized as strategies to meet demands rapidly in this economically evolving region.Request a custom research report for industry.
Dry Construction Market Analysis By Structure Type
Global Dry Construction Market, By Structure Type Market Analysis (2024 - 2033)
The Dry Construction market by structure type indicates that residential buildings lead with a market size of USD 1.24 billion in 2023, expecting to reach USD 2.30 billion by 2033. Commercial buildings garner USD 0.49 billion in 2023, projected to grow to USD 0.91 billion, while industrial spaces reflect a minor proportion, growing from USD 0.07 billion in 2023 to USD 0.13 billion by 2033.
Dry Construction Market Analysis By Material
Global Dry Construction Market, By Material Market Analysis (2024 - 2033)
In terms of material, Gypsum Products dominate the segment with a market value of USD 1.24 billion in 2023. Cement-Based Materials follow with USD 0.49 billion, while Insulating Materials represent a smaller segment at USD 0.07 billion. The market for Gypsum Products is projected to increase to USD 2.30 billion by 2033, while Cement-Based Materials and Insulating Materials are forecasted to grow correspondingly.
Dry Construction Market Analysis By Technique
Global Dry Construction Market, By Construction Technique Market Analysis (2024 - 2033)
Market analysis by construction technique highlights Modular Construction leading at USD 1.24 billion in 2023 and expected to double to USD 2.30 billion by 2033. Light Gauge Steel Framing follows suit, with anticipated growth reflecting rising popularity for its lightweight and economic advantages.
Dry Construction Market Analysis By End User
Global Dry Construction Market, By End-User Market Analysis (2024 - 2033)
In terms of end-users, the Construction Companies segment is the largest, constituting USD 0.93 billion in 2023, likely to reach USD 1.72 billion by 2033. This is indicative of growing contractor and builder reliance on dry construction practices for efficiency.
Dry Construction Market Analysis By Registration
Global Dry Construction Market, By Registration Type Market Analysis (2024 - 2033)
The market segment by registration type reveals Certified Providers leading at USD 1.47 billion in 2023, projected to reach USD 2.73 billion by 2033. This reflects escalating trust in certified systems within dry construction works, prioritizing quality and compliance.
Dry Construction Market Trends and Future Forecast
Request a custom research report for industry.
Global Market Leaders and Top Companies in Dry Construction Industry
Saint-Gobain:
A leading global producer of construction materials, Saint-Gobain specializes in innovative drywall products and integrated solutions, improving performance in sustainable construction.Knauf:
Knauf is a significant player in the dry construction sector, offering high-quality plasterboards and insulation solutions, committed to advancing sustainable building practices.USG Corporation:
USG Corporation is a pioneer in the production of drywall and related construction products, focusing on innovative techniques that enhance building performance and sustainability.We're grateful to work with incredible clients.
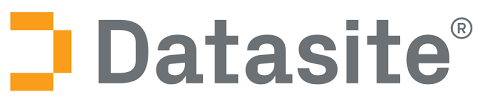
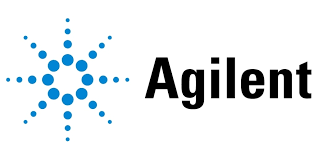

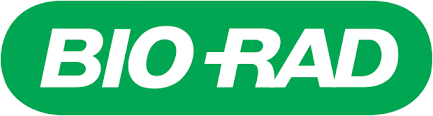
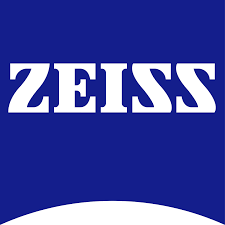
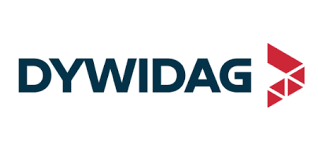
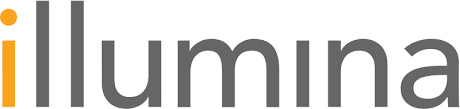
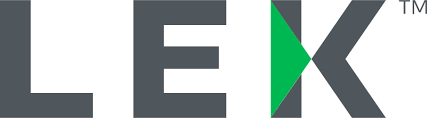
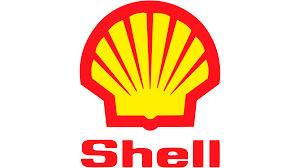
Related Industries
FAQs
What is the market size of dry Construction?
The dry construction market is valued at approximately $1.8 billion in 2023, with a projected CAGR of 6.2%. This substantial growth reflects increased demand for innovative building methods and sustainable materials.
What are the key market players or companies in the dry construction industry?
Key players in the dry construction market include leading construction firms, manufacturers of building materials, and suppliers of modular construction systems. Major companies are focused on sustainability and technological advancements in building practices.
What are the primary factors driving the growth in the dry construction industry?
Growth in the dry construction industry is driven by increasing urbanization, a shift towards sustainable building practices, and innovations in construction technology, enhancing efficiency and reducing material waste.
Which region is the fastest Growing in the dry construction market?
North America is projected to be the fastest-growing region within the dry construction market, showcasing a rise from $0.69 billion in 2023 to $1.29 billion by 2033, supported by robust infrastructural development.
Does ConsaInsights provide customized market report data for the dry construction industry?
Yes, ConsaInsights offers tailored market report data for the dry construction industry to meet specific business needs, enhancing decision-making processes through insightful and actionable data.
What deliverables can I expect from this dry construction market research project?
Deliverables from the dry construction market research project include comprehensive market analysis reports, trend assessments, competitive landscape data, and customized insights tailored to strategic planning.
What are the market trends of dry construction?
Current trends in the dry construction market include increased adoption of prefabricated building systems, growing popularity of eco-friendly materials, and technology integration for better project management and efficiency.