Closed Molding Composites Market Size, Share, Industry Trends and Forecast to 2033
This report provides a comprehensive analysis of the Closed Molding Composites market, focusing on market dynamics, size, growth forecasts, and regional insights from 2023 to 2033.
Metric | Value |
---|---|
Study Period | 2023 - 2033 |
2023 Market Size | $7.80 Billion |
CAGR (2023-2033) | 5.2% |
2033 Market Size | $13.09 Billion |
Top Companies | Hexcel Corporation, Toray Industries, Inc., Mitsubishi Chemical Corporation, SGL Carbon SE, Teijin Limited |
Last Modified Date | Invalid Date |
Closed Molding Composites Market Report (2023 - 2033)
Closed Molding Composites Market Overview
What is the Market Size & CAGR of Closed Molding Composites market in 2033?
Closed Molding Composites Industry Analysis
Closed Molding Composites Market Segmentation and Scope
Request a custom research report for industry.
Closed Molding Composites Market Analysis Report by Region
Europe Closed Molding Composites Market Report:
The European market is set to expand from $1.94 billion in 2023 to $3.25 billion by 2033, with strong demand for energy-efficient and lightweight materials across key industries.Asia Pacific Closed Molding Composites Market Report:
The Asia Pacific region is expected to show significant growth, with the market size projected to increase from $1.57 billion in 2023 to $2.64 billion by 2033. This growth is fueled by rising industrial activities and a growing demand for automotive composites.North America Closed Molding Composites Market Report:
North America remains a leading market with projections of growth from $2.52 billion in 2023 to $4.22 billion by 2033, primarily driven by the aerospace and automotive industries' demand for advanced composites.South America Closed Molding Composites Market Report:
In South America, the market is projected to grow from $0.78 billion in 2023 to $1.31 billion by 2033. The growth is supported by increased investments in infrastructure and wind energy sectors.Middle East & Africa Closed Molding Composites Market Report:
The Middle East and Africa market is expected to grow from $0.99 billion in 2023 to $1.67 billion by 2033, driven by increasing needs in the construction and automotive sectors.Request a custom research report for industry.
Closed Molding Composites Market Analysis By Product Type
Global Closed Molding Composites Market, By Product Type Market Analysis (2024 - 2033)
The Closed Molding Composites market, segmented by product type, includes thermosets which account for $6.78 billion in 2023, growing to $11.39 billion by 2033, holding an 86.97% market share. Thermoplastics constitute a smaller segment, with growth driven by their applications in various industries.
Closed Molding Composites Market Analysis By End User Industry
Global Closed Molding Composites Market, By End-User Industry Market Analysis (2024 - 2033)
In terms of end-user industries, the automotive sector is the largest, valued at $3.74 billion in 2023 and expected to grow to $6.29 billion by 2033, capturing 48.01% of the market share. Aerospace follows with significant growth due to technological advancements and increased usage of composites.
Closed Molding Composites Market Analysis By Application
Global Closed Molding Composites Market, By Application Market Analysis (2024 - 2033)
Applications of Closed Molding Composites span structural, aesthetic, and functional components. Structural components account for $5.28 billion in 2023, increasing to $8.87 billion by 2033, claiming a 67.74% market share.
Closed Molding Composites Market Analysis By Technology
Global Closed Molding Composites Market, By Technology Market Analysis (2024 - 2033)
Key molding technologies include manual and automated molding techniques. Manual molding dominates the market at $6.78 billion in 2023, rising to $11.39 billion by 2033, while automated molding shows growth potential with its efficiency.
Closed Molding Composites Market Analysis By Material
Global Closed Molding Composites Market, By Material Market Analysis (2024 - 2033)
The market's material segmentation includes resin infusion techniques, which are projected to grow from $5.28 billion in 2023 to $8.87 billion by 2033, maintaining a 67.74% share of the market.
Closed Molding Composites Market Trends and Future Forecast
Request a custom research report for industry.
Global Market Leaders and Top Companies in Closed Molding Composites Industry
Hexcel Corporation:
A leading global supplier of advanced composites that focuses on aerospace and industrial markets.Toray Industries, Inc.:
One of the largest manufacturers of advanced composite materials, focusing on carbon fiber production and thermoplastic composites.Mitsubishi Chemical Corporation:
A key player in the composites sector, known for its innovative approaches to materials used in the automotive and aerospace industries.SGL Carbon SE:
Recognized for its expertise in carbon fiber and composite materials, addressing various sectors including aerospace and automotive.Teijin Limited:
A pioneer in the field of advanced composites, focusing on sustainable production methods and innovative applications.We're grateful to work with incredible clients.
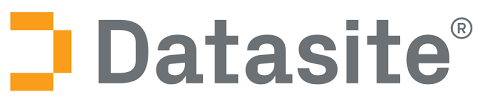
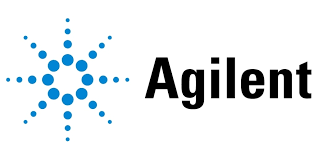

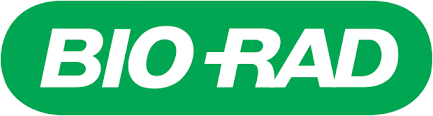
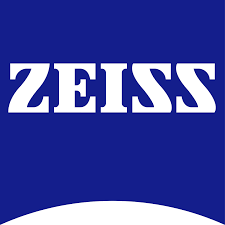
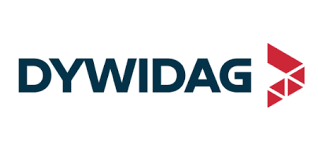
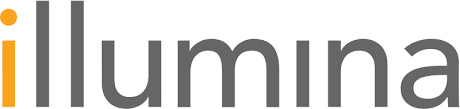
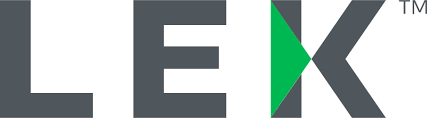
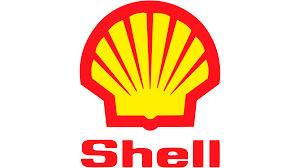
Related Industries
FAQs
What is the market size of Closed Molding Composites?
The Closed Molding Composites market is valued at $7.8 billion in 2023, with an expected CAGR of 5.2% from 2023 to 2033. This growth is fueled by increased demand across various industries and innovations in composite materials.
What are the key market players or companies in the Closed Molding Composites industry?
Key players in the Closed Molding Composites market include companies that specialize in advanced materials, production technologies, and innovative molding processes that drive efficiency and performance in applications like automotive and aerospace.
What are the primary factors driving the growth in the Closed Molding Composites industry?
Growth in the Closed Molding Composites industry is propelled by rising demand in industries such as automotive and aerospace, technological advancements, environmental regulations encouraging lightweight materials, and the increasing focus on sustainable manufacturing practices.
Which region is the fastest Growing in the Closed Molding Composites?
North America is currently the fastest-growing region in the Closed Molding Composites market, projected to increase from $2.52 billion in 2023 to $4.22 billion by 2033, driven by advancements in manufacturing and industry demands.
Does ConsaInsights provide customized market report data for the Closed Molding Composites industry?
Yes, ConsaInsights offers tailored market reports for the Closed Molding Composites industry, allowing clients to obtain specific insights that cater to their business needs and strategic goals.
What deliverables can I expect from this Closed Molding Composites market research project?
Expect detailed reports including market size, segmentation analysis, growth trends, competitive landscape, and regional insights, equipped with actionable data to inform strategic decisions in the Closed Molding Composites market.
What are the market trends of Closed Molding Composites?
Key trends in the Closed Molding Composites market include a shift towards automation, increasing use of recyclable materials, expanding applications in the automotive and aerospace sectors, and a growing emphasis on lightweight solutions for enhanced fuel efficiency.