Steel Processing Market Size, Share, Industry Trends and Forecast to 2033
This report provides an in-depth analysis of the Steel Processing market covering the period from 2023 to 2033. It includes market size, industry insights, trends, and forecasts, offering valuable data for stakeholders in the industry.
Metric | Value |
---|---|
Study Period | 2023 - 2033 |
2023 Market Size | $774.10 Billion |
CAGR (2023-2033) | 5.8% |
2033 Market Size | $1378.79 Billion |
Top Companies | ArcelorMittal, Nippon Steel Corporation, POSCO, Tata Steel |
Last Modified Date | Invalid Date |
Steel Processing Market Report (2023 - 2033)
Steel Processing Market Overview
What is the Market Size & CAGR of Steel Processing market in 2023?
Steel Processing Industry Analysis
Steel Processing Market Segmentation and Scope
Request a custom research report for industry.
Steel Processing Market Analysis Report by Region
Europe Steel Processing Market Report:
Europe's Steel Processing market is projected to grow from $237.18 million in 2023 to $422.46 million by 2033. Countries such as Germany and Italy lead in production advancements and sustainable processing methods contributing to the EU's green initiatives.Asia Pacific Steel Processing Market Report:
The Asia Pacific region demonstrates significant growth in the Steel Processing market, projected to increase from $148.16 million in 2023 to $263.90 million by 2033. Key countries like China, India, and Japan are leading producers, bolstered by substantial investments in infrastructure and manufacturing.North America Steel Processing Market Report:
North America shows a robust market size, increasing from $262.42 million in 2023 to $467.41 million by 2033. The United States remains the dominant player due to its advanced technological capabilities and a stable growing economy in construction and energy sectors.South America Steel Processing Market Report:
The South American Steel Processing market is expected to grow from $56.20 million in 2023 to $100.10 million by 2033. Brazil and Argentina are key markets with ongoing developments in their respective construction and automotive sectors driving demand.Middle East & Africa Steel Processing Market Report:
The Middle East and Africa market is anticipated to grow from $70.13 million in 2023 to $124.92 million by 2033, driven by growing construction activity in regions like the UAE and South Africa, focusing on infrastructure enhancement and economic diversification.Request a custom research report for industry.
Steel Processing Market Analysis By Product
Global Steel Processing Market, By Product Market Analysis (2024 - 2033)
The market for flat products is substantial, showing a significant increase from $511.68 million in 2023 to $911.38 million by 2033, maintaining a market share of 66.1%. Long products follow, with growth from $212.03 million to $377.65 million, comprising approximately 27.39% of the market. Pipes and tubes, accounting for 6.51% of the share, reflect growth from $50.39 million to $89.76 million, indicating their rising importance in construction and energy sectors.
Steel Processing Market Analysis By Technique
Global Steel Processing Market, By Technique Market Analysis (2024 - 2033)
The casting industry reveals a dominant size of $511.68 million in 2023, increasing to $911.38 million by 2033, holding a significant market share. Forging techniques, valued at $212.03 million, are set to grow to $377.65 million, while rolling techniques account for a smaller piece of the market yet are essential for producing specific types of steel, increasing from $50.39 million to $89.76 million.
Steel Processing Market Analysis By Application
Global Steel Processing Market, By Application Market Analysis (2024 - 2033)
The construction industry remains the largest application sector, projected to rise from $401.68 million in 2023 to $715.45 million in 2033, comprising about 51.89% of the market share. The automotive sector is also significant, expected to grow from $185.71 million to $330.77 million, with aerospace and shipbuilding contributing competitively to market dynamics, indicating diverse application reliance on steel processing.
Steel Processing Market Analysis By End User
Global Steel Processing Market, By End-User Industry Market Analysis (2024 - 2033)
Key end-user industries for processed steel include construction, automotive, and energy. In construction, steel processing shows growth from $334.18 million in 2023 to $595.22 million by 2033. The automotive segment is noteworthy too, with a rise from $174.79 million to $311.33 million. These segments underline the steel market’s vital role in supporting infrastructure and transport sectors.
Steel Processing Market Analysis By Finish Type
Global Steel Processing Market, By Finish Type Market Analysis (2024 - 2033)
Finished steel products dominate with a market size growing from $678.11 million in 2023 to $1,207.82 million by 2033, maintaining a substantial share of 87.6%. Semi-finished steel also holds significant value, with an anticipated increase from $95.99 million to $170.97 million, showcasing essential processes required in steel production.
Steel Processing Market Trends and Future Forecast
Request a custom research report for industry.
Global Market Leaders and Top Companies in Steel Processing Industry
ArcelorMittal:
The world's leading steel and mining company, inspiring sustainable steel solutions and leading in technology-driven innovation.Nippon Steel Corporation:
A major player in steel production, recognized for its leading position in the Asia-Pacific region and continuous development of high-performance steel.POSCO:
South Korea's leading steel manufacturer, noted for its advanced processing capabilities and commitment to eco-friendly practices.Tata Steel:
One of the largest steel manufacturers globally, Tata Steel is known for its diversified product range and innovative steel processing techniques.We're grateful to work with incredible clients.
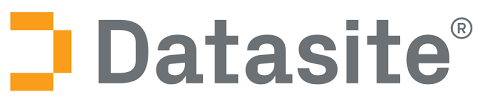
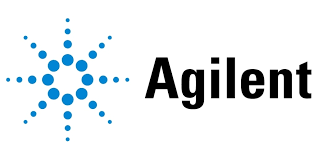

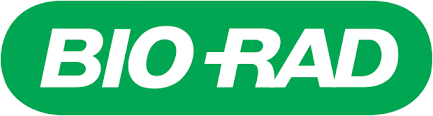
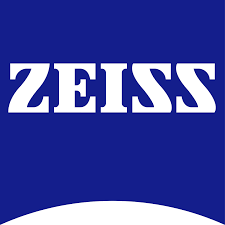
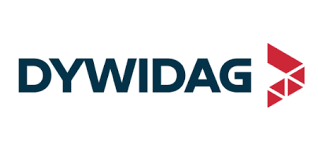
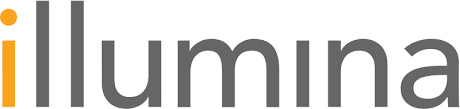
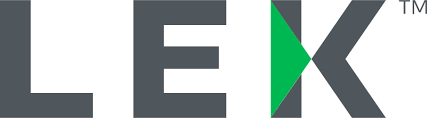
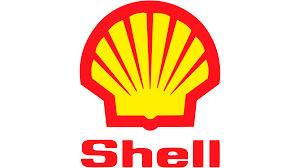
Related Industries
FAQs
What is the market size of steel Processing?
The global steel processing market is valued at approximately $774.1 billion as of 2023 and is expected to grow at a CAGR of 5.8%, reaching approximately $1,354.6 billion by 2033.
What are the key market players or companies in the steel Processing industry?
Key players in the steel processing market include Tata Steel, ArcelorMittal, Nippon Steel Corporation, POSCO, and Nucor Corporation, each dominating various segments from flat products to specialized steel processes.
What are the primary factors driving the growth in the steel Processing industry?
Growth is driven by rising infrastructure projects, increasing demand in the automotive sector, regional industrialization, advancements in processing technologies, and investments in sustainable steel production methodologies.
Which region is the fastest Growing in the steel Processing?
Asia Pacific is the fastest-growing region, with market size forecasted to rise from $148.16 billion in 2023 to $263.90 billion by 2033, reflecting significant industrial growth and infrastructure development.
Does ConsaInsights provide customized market report data for the steel Processing industry?
Yes, ConsaInsights offers customized market reports tailored to specific needs within the steel-processing industry, ensuring relevant insights, data segmentation, and regional analyses.
What deliverables can I expect from this steel Processing market research project?
Expect comprehensive reports detailing market sizes, growth forecasts, competitive analysis, segmentation data, key player profiles, and regional insights customized to your specifications.
What are the market trends of steel Processing?
Trends include a shift towards eco-friendly steel production, increasing automation in processing, rising demand for high-strength steel in automotive and construction, and consolidation among major players.