Metal Injection Molding Market Size, Share, Industry Trends and Forecast to 2033
This report offers a comprehensive analysis of the Metal Injection Molding (MIM) market, covering insights into growth factors, trends, and forecasts from 2023 to 2033.
Metric | Value |
---|---|
Study Period | 2023 - 2033 |
2023 Market Size | $5.20 Billion |
CAGR (2023-2033) | 6.3% |
2033 Market Size | $9.73 Billion |
Top Companies | ARC Group Worldwide, Hoganas AB, PTI - Precision Technology, Inc. |
Last Modified Date | Invalid Date |
Metal Injection Molding Market Report (2023 - 2033)
Metal Injection Molding Market Overview
What is the Market Size & CAGR of Metal Injection Molding market in 2023 and 2033?
Metal Injection Molding Industry Analysis
Metal Injection Molding Market Segmentation and Scope
Request a custom research report for industry.
Metal Injection Molding Market Analysis Report by Region
Europe Metal Injection Molding Market Report:
Europe’s market for Metal Injection Molding is highlighted by its strong industrial base, currently valued at $1.25 billion in 2023 and expected to grow to $2.34 billion by 2033, driven by technological advancements and increasing applications in medical devices and automotive industries.Asia Pacific Metal Injection Molding Market Report:
The Asia-Pacific region is projected to be one of the fastest-growing markets for Metal Injection Molding, with a market size of $0.99 billion in 2023, expected to reach $1.85 billion by 2033. This growth is primarily driven by increasing automotive production and electronic components manufacturing in countries like China, Japan, and South Korea.North America Metal Injection Molding Market Report:
North America has a significant market presence, with a size of $1.95 billion in 2023, projected to grow to $3.65 billion by 2033. The region is seeing strong demand from the automotive and aerospace sectors, where precision and lightweight components are increasingly necessary.South America Metal Injection Molding Market Report:
In South America, the Metal Injection Molding market is smaller but shows promise with a market size of $0.35 billion in 2023, expected to reach $0.65 billion by 2033. Key drivers include rising demand for consumer electronics and automotive parts in Brazil and Argentina.Middle East & Africa Metal Injection Molding Market Report:
The Middle East and Africa present a growing market opportunity, starting at $0.67 billion in 2023 and anticipated to reach $1.24 billion by 2033. Increased investments in infrastructure and manufacturing capabilities in the GCC countries are key facilitators of growth.Request a custom research report for industry.
Metal Injection Molding Market Analysis By Material Type
Global Metal Injection Molding Market, By Material Type Market Analysis (2024 - 2033)
The MIM market is largely driven by stainless steel, representing 54.1% of the market share in 2023 with sales of $2.81 billion, projected to reach $5.26 billion by 2033. Carbon steel and copper alloys also play a role, having market shares of 22.13% and 10.42%, respectively.
Metal Injection Molding Market Analysis By Application
Global Metal Injection Molding Market, By Application Market Analysis (2024 - 2033)
The automotive industry leads the MIM market share at 54.1%, with a size of $2.81 billion in 2023, and forecasted to grow to $5.26 billion by 2033. The electronics sector follows, showing strong growth potential as demand for miniaturized components rises.
Metal Injection Molding Market Analysis By Process
Global Metal Injection Molding Market, By Process Market Analysis (2024 - 2033)
Powder Injection Molding dominates the market, accounting for 88.25% of market share, valued at $4.59 billion in 2023 and set to reach $8.59 billion by 2033. Capillary Molding is emerging, with increasing interest due to its advantages in specific applications.
Metal Injection Molding Market Analysis By End User
Global Metal Injection Molding Market, By End-User Industry Market Analysis (2024 - 2033)
The medical devices sector is showing growth, currently at $0.54 billion in 2023 and expected to grow significantly by 2033, due to increased healthcare demands and the need for precision-engineered components in medical technology.
Metal Injection Molding Market Analysis By Region
Global Metal Injection Molding Market, By Region Market Analysis (2024 - 2033)
Regional analysis highlights North America and Europe as leading markets, but significant opportunities are present in Asia-Pacific due to manufacturing expansion. The Middle East and Africa are also seeing growth, driven by investments in industrial capabilities.
Metal Injection Molding Market Trends and Future Forecast
Request a custom research report for industry.
Global Market Leaders and Top Companies in Metal Injection Molding Industry
ARC Group Worldwide:
A comprehensive provider of innovative manufacturing solutions, ARC Group Worldwide leverages advanced MIM technologies to deliver precision components across multiple industries.Hoganas AB:
Hoganas is recognized for its expertise in powder metallurgy and MIM, producing high-density, high-strength components designed for various applications in the automotive and medical fields.PTI - Precision Technology, Inc.:
A leader in MIM services, PTI specializes in precise and intricate part production for diverse industries, emphasizing customer collaboration during the design and manufacturing process.We're grateful to work with incredible clients.
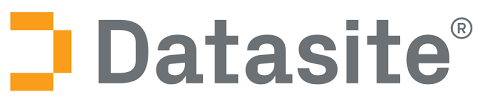
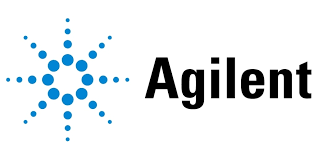

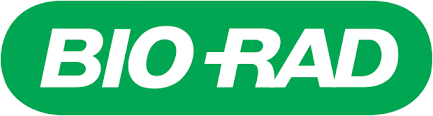
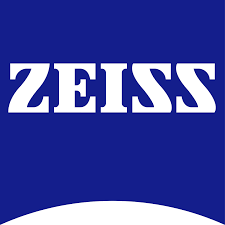
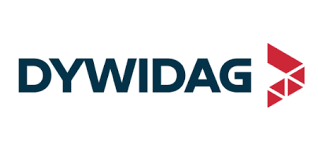
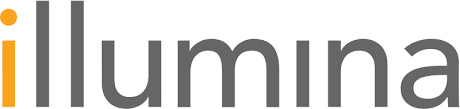
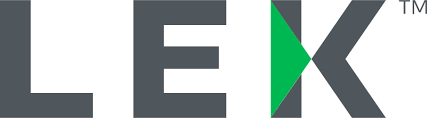
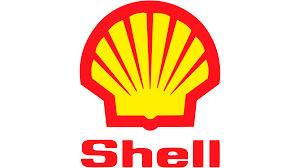
Related Industries
FAQs
What is the market size of Metal Injection Molding?
The global metal injection molding market is valued at approximately $5.2 billion in 2023 and is projected to grow with a CAGR of 6.3%, reaching a significant market size by 2033 as manufacturing demands rise.
What are the key market players or companies in this Metal Injection Molding industry?
Key players in the metal injection molding sector include companies like Indo-MIM, PSP Technologies, and ARC Group Worldwide, which are pivotal in driving innovations and expanding their capacities to meet increasing industry demands.
What are the primary factors driving the growth in the Metal Injection Molding industry?
Growth in the metal injection molding market is driven by increasing demand for complex geometries in automotive and aerospace sectors, advancements in technology, and heightened demand for lightweight materials to improve efficiency and reduce costs.
Which region is the fastest Growing in the Metal Injection Molding?
The Asia-Pacific region is the fastest-growing market in metal injection molding, anticipated to grow from $0.99 billion in 2023 to $1.85 billion by 2033, driven by industrialization and increased manufacturing activities.
Does ConsaInsights provide customized market report data for the Metal Injection Molding industry?
Yes, ConsaInsights offers customized market reports that provide tailored data and insights specific to the metal injection molding industry, catering to the unique needs and queries of clients.
What deliverables can I expect from this Metal Injection Molding market research project?
Expect comprehensive deliverables including market size analysis, growth projections, competitive landscape assessments, and trend analysis, all aimed at providing crucial insights to inform strategic decisions.
What are the market trends of Metal Injection Molding?
Current trends in the metal injection molding market include increased adoption in consumer electronics, advancements in sustainability practices, and a shift towards automated manufacturing processes to enhance production efficiency.